Öntészet

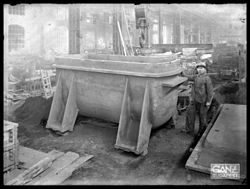
Az öntészet (formaöntés) vagy fémöntés lényege az, hogy elkészítenek egy olyan üreget, ami a munkadarab negatívját tartalmazza (ezt formának nevezik), az üregbe megolvasztott fémet öntenek, majd hagyják megdermedni. Az öntészet mint tudomány foglalkozik a forma- és magkészítés anyagaival, az öntött fémek sajátságaival, az öntési folyamat jellemzőivel, az öntészeti olvasztókemencékkel és öntőgépekkel, az öntött termék tulajdonságaival stb.
Öntéssel változatos és bonyolult alakú fémtermékek állíthatók elő. Az öntészet termékei például a belső égésű motorok motorblokkjai, szivattyúházak, víz- és gázszelepek, fürdőkádak és ajtókilincsek stb.
A fémöntés és a formakészítés technológiája szerint a következő eljárásokat különböztetjük meg:
- öntés homokformázással,
- precíziós öntés,
- keramikus formázás,
- kokillaöntés.
Homokformázás
[szerkesztés]Nyers homokformázás
[szerkesztés]


Homokformázáskor a forma készítésére agyagkötésű homokot használnak. A formaüreget minta segítségével készítik el. A minta a munkadarab zsugorméretekkel és öntési ferdeséggel kiegészített (néha beömlő rendszerrel készült) mása. A minta általában többször használatos, de készülnek ún. elvesző minták is (például viaszból). Amennyiben az öntvény üreges, az üregek helyére magokat helyeznek, azok pontos elhelyezéséről magjelekkel gondoskodnak. A folyékony fémet a beömlő rendszeren keresztül juttatják a formaüregbe. Az öntés során keletkező gázok elvezetéséről légzőfuratokkal, a dermedés közbeni zsugorodás miatti fémutánpótlásról tápfejjel vagy felöntéssel gondoskodnak.
A forma általában többrészes, leggyakrabban két részből áll. A formakészítés az alsó formafél elkészítésével kezdődik. A mintát (illetve annak osztófelülettel osztott felét) és a formaszekrényt ráhelyezik egy formázólapra. Az osztófelület lehet sík, vagy ha a darab alakja megkívánja, tört felület is. A formaszekrényt kitöltik formahomokkal és tömörítik (döngöléssel, rázással, sajtolással stb.). Miután elkészült az alsó formafél, megfordítják, ráhelyezik a felső formaszekrényt és a felső mintafelet. Gondoskodnak a beömlő rendszerről és a felöntésről, majd ezt a formafelet is kitöltik homokkal és tömörítik. A felső formafelet leemelik, kiveszik a mintákat és behelyezik a magokat, majd a felületek védelmére, illetve a ráégések elkerülése érdekében védőanyaggal vonják be. A védőanyag neve fekecs, és általában grafit, homok, olaj és víz keveréke. Fekecselést elsősorban nagyobb olvadáspontú fémek öntésekor alkalmaznak. A formafeleket illesztőcsapok segítségével összeillesztik, majd súlyokkal leterhelik, hogy a folyékony fém ne tudja szétválasztani a formafeleket. Nagyobb méretű öntvények esetén öntés előtt a formát kiszárítják.
A folyékony fém formába öntésére különös gondot kell fordítani, mert az áramló fém ereje kárt tehet a formában és a magokban. Ezt elsősorban a beömlő rendszer megfelelő tervezésével és kivitelezésével lehet kiküszöbölni. Az öntvény zsugorodása során jelentkező fémhiány pótlására tápfejeket helyeznek el az öntvény nagyobb keresztmetszetű részeinél.
Az öntés alapja a jó minta, elkészítését mindig kiváló szakemberek végzik. A minták többnyire osztott kivitelben készülnek, ezért a pontos összeillesztésről csapokkal gondoskodnak. Méreteiket a zsugorodás figyelembe vételével tervezik meg. A mintának üreges öntvény esetén tartalmaznia kell a magjeleket is, azokat a formában kialakítandó részeket, amelyek a magok pontos és biztos elhelyezését biztosítják. A minta eltávolíthatósága érdekében a mintán – az osztófelület felé mutató – oldalferdeséget kell kialakítani. Az oldalferdeség mértéke kézi formázás esetén 1–3°, gépi formázáskor 0,5–1°. A minta készülhet rétegelt fából, műanyagból és fémből. Felületét lakkozással, festéssel védik az igénybevételtől.
Vegyi kötésű homokformázás
[szerkesztés]A vegyi kötésű homokformázást a homokforma szilárdságának fokozási igénye hívta életre. A különböző vegyi kötések alkalmazása miatt gyakran a szükségtelenné válik a homoktömörítés. A vegyi kötésű homokformázáshoz a következő technológiák tartoznak:
- Széndioxid-vízüveg kötésű homokformázás: A homokhoz 4–8% vízüveget kevernek, a kész formán pedig szén-dioxidot áramoltatnak át. A vízüveg és a szén-dioxid egymásra hatása révén szilikagélháló jön létre a felületeken, ami jelentős szilárdságjavulást eredményez.
- Műgyanta kötésű homokformázás: Ebben az esetben 2%-nyi műgyantát adnak a homokhoz, a keményítést melegítéssel vagy vegyi módszerekkel érik el.
- Héjformázás: A héjformázást bonyolult alakú, vékony falú öntvények készítésekor használják. A héjformázás tulajdonképpen formaszekrény nélküli formázás, amelynél a homokszemcséket fenolformaldehid gyanta és hexametilén-tetramin keverékből álló bevonat veszi körül. Ezt a homokot meleg fémmintára öntik, így egy bizonyos vastagságú réteg tapad meg rajta. Az egészet kemencében hevítik, amitől a héj megszilárdul. A fém mintát eltávolítják, a kettévágott héjat újból összeerősítik, homokba ágyazzák és öntenek.
Precíziós öntés
[szerkesztés]Precíziós öntésnél a minta alapanyaga viasz, amelyet fém, vagy speciális gumi mesterformába sajtolással állítanak elő. A viasz mintákat hasonló anyagú és fürtös alakú közös beömlő rendszerre erősítik (bokrosítás). A formázás folyékony formázóanyagba való ismételt mártogatásból és szárításból áll. A formázóanyag általában szilikátpor tartalmú emulzió. A réteg hizlalását addig folytatják, míg el nem éri a 2–10 mm vastagságot. Ezután durvább szemcséket tartalmazó formázóanyagba mártogatják, majd a végleges vastagság elérése után kiolvasztják a viaszt, az üres kéregformákat pedig kiégetik. Öntéshez a formákat homokba ágyazzák és kiöntik folyékony fémmel. Precíziós öntéssel változatosabb alakú és pontosabb, jobb felületű öntvények állíthatók elő, de csak kisebb darabok esetén alkalmazható.
Viaszveszejtéses öntés
[szerkesztés]A viaszveszejtéses vagy viaszvesztéses eljárás – a precíziós öntés változata – évszázadokkal ezelőtt alakult ki, és elsősorban az ötvösség és a szobrászat területén alkalmazták előszeretettel. A viaszból kézzel mintázott egyedi műtárgy – ékszer, érem, plakett, kisplasztika, szobor – hűen visszaadja alkotója keze munkáját. Olyannyira, hogy gyakran még a művész ujjlenyomata is felfedezhető az öntvényen. Az így létrehozott alkotáson nem jelennek meg a legtöbb öntészeti eljárásra jellemző osztófelületek melletti kitüremkedések, sorják, így a végső megmunkálás, a cizellálás sokkal kevesebb munkát igényel. Ezzel az ősi eljárással napjainkban is rendszeresen készülnek egyedi műtárgyak. Magyarországon elsősorban az ötvösség és az éremművészet területén alkalmazzák, de készülnek egyedi kisplasztikák is szép számmal ezzel az eljárással. Virtuóz mestere volt Ligeti Erika szobrász és éremművész, de a ma élő alkotók közül jelentősek Kótai József, Soltra E. Tamás, Szabó György, Szöllőssy Enikő, Szunyogh László így készült művei is.
Az eljárás menete a forma elkészítésével kezdődik, általában tűzálló anyagból (gipsz, samott, homok keveréke). A kész formát olyan vastagon vonják be viaszréteggel, amilyen vastagra a kész szobrot tervezik. A viaszréteghez csőhálózatot illesztenek, amely a későbbiekben elvezeti a megolvadt viaszt és a gázokat. A viaszszobor felületét agyaggal borítják úgy, hogy a csövek vége a szabadba nyíljon. Ezután a szobrot kiégetik, melynek során a viaszréteg kifolyik. A viasz helyén keletkezett résbe vagy üregbe beleöntik a folyékony bronzot, majd annak kihűlésekor az agyagformát széttörik, és a bronzfelületet szükség szerint díszítik (cizellálják).
Keramikus formázás
[szerkesztés]A keramikus formázás célja nagy hőállóságú forma létrehozása. Ehhez cirkon és timföld kötőanyag keverékét öntenek egy mintára. Száradás után a formát leválasztják a mintáról és kiégetik. Ezután a forma feleket összeillesztik és kiöntik.
Kokillaöntés
[szerkesztés]
A kokillák fémből, általában acélból készült öntőformák. A kokillaöntés módszerei:
- gravitációs kokillaöntés,
- kiszorításos kokillaöntés,
- nyomásos öntés.
Gravitációs kokillaöntés
[szerkesztés]A legegyszerűbb kokillaöntési módszer, már régóta alkalmazott technológia. A kokillákat forgácsolással készítik, a felületeken 0,5–2°-os oldalferdeséget alkalmaznak. Előnye a homokformába öntéssel szemben a pontosabb méret, a jobb felület és a lényegesen nagyobb munkatermelékenység.
Kiszorításos kokillaöntés
[szerkesztés]A módszer alkalmazásakor a nyitott alsó kokillába beöntik az olvadt fémet, majd a felső kokillát az alsóhoz préselik, miközben az olvadt fém felveszi a kokillaüreg alakját és jelentős nyomás alá kerül. A kiszorításos kokillaöntés egyesíti az öntés és a kovácsolás sajátosságait. Színesfém szerelvények (pl. fürdőszoba csaptelepek) gyártásában és az autóiparban használják.
Nyomásos öntés
[szerkesztés]
Nyomásos öntés esetén öntőgépen, többrészes kokillába történik az öntés. Az öntőgép nyitja és zárja a szerszámfeleket, az olvadt fémet pedig belövi a kokillába. Elsősorban alumínium, magnézium és más kisebb olvadáspontú fémek öntésére használják. Nagy termelékenységű öntési eljárás, egy gép óránként akár több mint 10 000 darab öntvény előállítására is képes. Gépkocsik, iroda- és számítógépek, kéziszerszámok stb. alkatrészei készülnek nyomásos öntéssel. Előnye az eljárásnak a nagy termelékenység, a nagy pontosság és a kiváló felületi minőség.
Olvasztó berendezések
[szerkesztés]- Tégelykemencék: Az olvasztandó fémet általában grafitból készült tégelyben olvasztják meg. A fűtés földgázzal vagy elektromos módszerrel történik. A fémfürdő felületét sóolvadék réteggel vagy védőgázzal, esetleg vákuummal védik meg az oxidációtól.
- Ívkemencék: A fémet az elektromos ív hőhatásával olvasztják meg, főleg ötvözött acélöntvények anyagának készítésére használják.
- Kupolókemencék: Aknás típusú kemence, a legrégebben használt típus az öntödékben. Az alapanyagot (nyersvasat, kokszot) felülről adagolják, levegőt fújnak be, a megolvadt vasanyagot és a salakot külön csapolják.
- AOD (Argon Oxygen Decarburization) konverterek: A konverterben lévő vasfürdőt a befúvatott argon–oxigén–nitrogén gázkeverék állandó keverésben tartja, amivel meggyorsulnak a redukciós folyamatok. Főleg alacsony szén- és szennyezőtartalmú saválló acélok gyártásakor használatos.
Források
[szerkesztés]- Nándori Gyula – Vereskői János: Vas-, acél- és fémöntészet. Budapest: Tankönyvkiadó. 1977.
- Öntészeti kézikönyv. Varga Ferenc (szerk.). Budapest: Műszaki Könyvkiadó. 1985.
- Imrehné Sebestyén Margit: A képzelet világa 9. Apáczai Kiadó, 2013.
További információk
[szerkesztés]- Öntészet.lap.hu - linkgyűjtemény
- Az öntés folyamata, plasztikum.hu